-
Support for ODMDo you find your product unsatisfactory? Are the colors mixed? Is the output unstable? Let our experienced engineering team design a screw that meets your high-performance and wear-resistant requirements. What is screw design? Regardless of your application or process, working with Chuangri can meet your production needs. The feed screw design process begins with our engineering experts collaborating with you to design a new feed screw, barrel, or component that precisely meets your requirements. Our feed screw design resources are incredibly valuable to your business. With years of experience and specialized manufacturing knowledge, our feed screw designers can provide suggestions to improve efficiency and performance, ultimately achieving better performance metrics and higher productivity. Optimal Screw Design
-
Support for OEMWith over 30 years of experience in the extrusion/injection molding field, we have maintained long-term supply partnerships with hundreds of well-known domestic and international extrusion and injection molding machine brands. We can process according to your provided machine models and drawings. Our unique wear-resistant protection technology helps extend the life of extrusion and injection molding machines, improve productivity, and enhance the quality of end products, helping you achieve greater success in the markets you serve.
CUSTOM We Support Customization
Did you know that issues in extrusion or injection molding processes may arise due to an incomplete match between the screw and the application? From metal alloys to finished products, we offer one-stop production services for screws and barrels. Different screw designs are intended to achieve specific processing effects. Therefore, customizing the right screw can improve productivity and reduce waste. Let us assist you in maximizing both your production and profits.
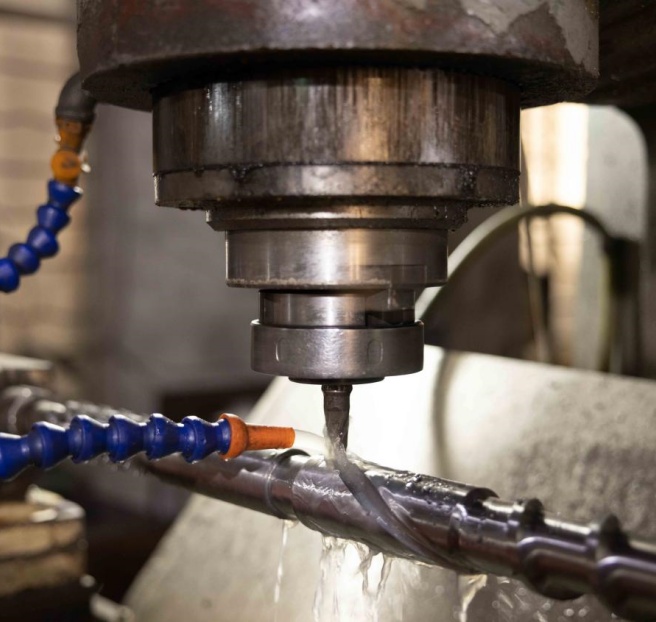
GOREANMENT Choose Your Materials
With years of experience in the plastic machinery industry, Chuangri has extensive knowledge of different nitrided and alloy steels. We leverage the functionalities of various steels to select the most suitable raw materials for you.
-
38CrMoAlA AISI 4140 D2 NITRALLOY 135-M H13 2344General Steel Materials
-
AISI 4340 42CrMo DC53 AISI 8620 SKD61 40CrAlloy Steel
-
CPM 10V CPM 9V CPM S90V HASTELLOY C-276 INCONELSolid Carbide
-
300 STAINLESS 304 STAINLESS 316 STAINLESS 430 STAINLESS 17-4 PH STAINLESSStainless Steel
-
Standard Steel
SCREW AND BARREL Professional Customization, Efficient Delivery, Achieving Your Production Goals!
From intricate geometries to specialized materials and performance requirements, our expert team leverages advanced technologies to meet your precise needs. We provide comprehensive solutions from initial planning to final delivery, empowering your equipment to operate at its peak efficiency.
-
01Requirement Analysis and Data Collection
-
02CAD/CAE Engineering Design
-
03Material Selection and Production
-
04Testing and Inspection of Every Detail
-
05Packaging and Logistics Services
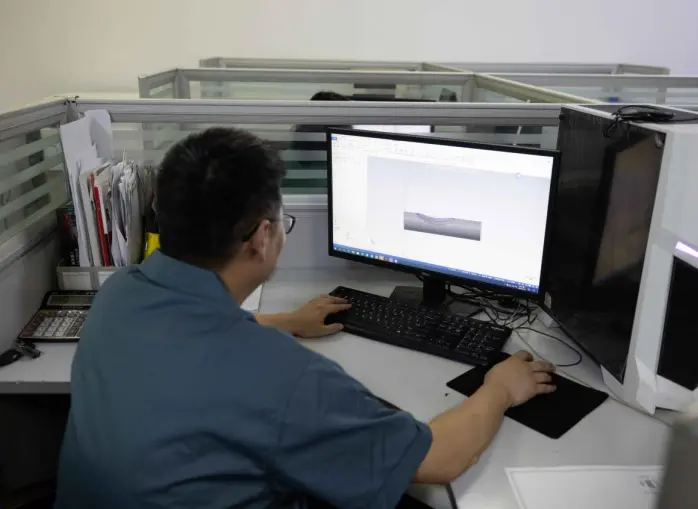
Processing Techniques Nitriding, Bimetallic, Quenching, and Coating.
-
Nitriding ProcessNitriding is a heat treatment process conducted in a gaseous mixture of nitrogen and hydrogen. The temperature is elevated to 930–1100ºF (500–593ºC), initiating the nitriding reaction. Plasma is diffused onto the metal surface, forming a nitrided layer within the screws that contains chromium nitride (CrN). This composition provides exceptional thermal stability, enabling the screws to withstand the high temperatures generated during plastic extrusion or molding processes. With a maximum hardness of 65–70 HRC, screws made from these materials are highly resistant to wear, even in extremely demanding applications.
-
Barrel Alloying ProcessThe centrifugal casting process involves heating metal in a high-temperature furnace to temperatures exceeding 2000°F. Once the alloy is melted, a covered cylindrical mold is placed on casting rollers and rotated at high speeds. This ensures uniform distribution of the molten alloy in terms of thickness, hardness, and density. After cooling, the cover is removed, and the barrel is machined to the finished specifications. The inlay or outer layer of bimetallic liners is typically ground to a thickness of 0.060–0.080 inches. We offer customization to suit your production environment, providing corrosion-resistant alloys, high-nickel content, tungsten carbide, high-carbon alloys, corrosion-resistant nickel, nickel-rich iron/boron alloys, and dozens of other specialized alloy options.
-
Quenching ProcessScrew quenching is a heat treatment process designed to enhance the surface hardness and strength of screws. The fundamental principle involves heating the screw to a specific high-temperature range, followed by rapid cooling. This induces a martensitic transformation in the screw's surface metal, forming a hardened layer. Screws are typically heated to quenching temperatures of 1000–1100°C. Post-quenching, screws usually undergo tempering treatment, which involves reheating to a lower temperature range (typically 150–250°C) for a set duration. This step alleviates internal stresses introduced during the quenching process, reducing the risk of brittleness or cracking during operation. In high-stress and high-temperature applications, quenched screws demonstrate significantly improved performance in harsh environments, effectively extending the lifespan of the equipmen
-
Electroplating CoatingElectroplating typically includes two main types: chromium plating and titanium plating. Chromium plating is an electroplating process that deposits a layer of chromium metal onto the surface of a substrate. The chromium layer usually ranges in thickness from 10 to 50 microns and offers excellent adhesion and wear resistance, enhancing surface smoothness and durability. Titanium plating is an electrochemical process that applies a layer of titanium metal or titanium alloy onto the surface of screws. This coating is particularly suitable for screws used in high-temperature and highly corrosive environments
CUSTOMIZATION How to Customize
-
Submit your machine information and connection dimensions, along with a brief description of your needs.
Prepare a set of calipers and a tape measure, and simply provide us with your extruder/injection molding machine nameplate and connection dimension table.
Our team will communicate with you to understand your screw and barrel size information, the products being produced, the materials used, and your specific requirements (e.g., higher output or longer lifespan).01/04 -
Receive a quotation and feedback
After receiving your request, we will review it within 3 hours and provide feedback. Our team will consult you on materials, technical processes, and modifications that can make your concept manufacturable, along with a quote.02/04 -
Create drawings and revision checks
Our engineering team will provide assembly drawings of the screw and barrel within 2 days. We will double-check these against your machine to ensure all dimensions match, avoiding installation issues.03/04 -
Pay the deposit and commence production
Upon receiving your deposit as agreed in the contract, we will begin production within 1-2 days. The efficiency is based on our advanced equipment and annual production capacity. We can deliver your custom screws and barrels in optimal condition within 30 to 40 days.04/04