How Extruder Screw and Barrel Design Impacts Output Quality
How Extruder Screw and Barrel Design Impacts Output Quality
Exploring the Impact of Extruder Screw and Barrel Design
The Role of Extrusion Screw Barrel in Manufacturing
The extrusion screw barrel has a significant place in plastic and rubber product industries. Screw barrels are designed to serve various applications such as manufacturing pipes, sheets, films, wire drawing and granulation. Different types of screws (e.g., barrier, vented, or separation designs) achieve maximum efficiency for specific materials, such as engineering plastics, PVC blends and rubber. Bimetal screw barrels are equipped with a 1—5mm alloy layer on the inner barrel wall, offering increased wear resistance, corrosion resistance and heat resistance. This enhances service life significantly over nitrided barrels, especially in processing abrasive products like calcium-rich PVC. CHUANGRI SCREW has specialized in producing screw cylinders to upgrade manufacturing efficiency with more than two decades of experience in the field. The company is committed to a strategy of product designing by integrating design and manufacturing and providing top-notch customer service to provide highest quality and customer satisfaction.
Key Features of CHUANGRI SCREW’s Extruder Screw and Barrel
CHUANGRI SCREW deals in the production of long-life and high-performance extruder barrels and screws that demonstrate their commitment to production processes and quality as well as excellence.
Durable Material Construction
Bimetal barrels feature a 1—5mm alloy coating for superior wear, corrosion and high-temperature resistance, they are ideal for abrasive materials like calcium-rich PVC. Nitrided variants offer hardened surfaces for general applications. Screws use High-Velocity Oxygen Fuel (HVOF) and Plasma Transferred Arc (PTA) welding techniques to reinforce flight tips to enhance longevity in demanding conditions.
Customizable Designs
Screw diameters range from Ø15–Ø600mm with adjustable L/D ratios to suit diverse extrusion needs such as pipes, films and recycling. Options include barrier, vented, separation and pinned screws, optimized for materials like engineering plastics, rubber and recycled polymers.
High-Performance Applications
Tailored designs for PP, PE, PET and PA recycling, including water-fed and side-feeding systems for films and woven bags. And precision-machined screws with nitriding or chromium plating for ABS, PC and other thermoplastics.
Enhancing Output Quality with Advanced Designs
How Design Affects Product Consistency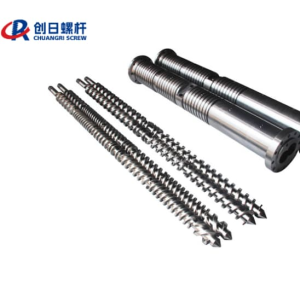
The way an extruder screw and barrel are designed plays a role in the quality of the final product outcome at CHUANGRI SCREW. Take the Parallel Twin-Screw Barrel for example, they utilize the advanced technology to guarantee top-notch plasticization performance from their components by using materials like 38CrMoAlA for their blown film machine barrels and screws that strike a balance between hardness post-quenching and nitridation, thereby improving both durability and output quality levels through meticulous design attention to ensure consistency across various production runs.
Improving Efficiency with CHUANGRI SCREW Solutions
Efficiency is a focus of CHUANGRI SCREW products and services. Their extrusion screw barrels are crafted to handle a wide range of materials. From common plastics such as PP and PE to more specialized ones like engineering plastics and fluoride plastics. CHUANGRI SCREW delivers tailored solutions that ensure optimal performance across various applications. Their bimetallic screw and barrel options offer improved resistance to wear and tear making them perfect for demanding applications.
The Science Behind Barrel Screw Extruders
The Mechanics of Barrel Screw Extruders
The barrel screw extruders are used in pipe extrusion, film blowing, sheet production and granulation with screw types optimized for each process. For example, the vented screws for degassing, barrier screws for melt uniformity. The way barrel screw extruders work is crucial to their role in manufacturing processes at CHUANGRI SCREW, where they prioritize the design and engineering of these parts above all else. With a single-minded approach to producing high-quality screw and barrel components with precise dimensions that allow for effective material processing. Their approach involves optimizing the length-to-diameter ratio and employing cutting-edge materials that can withstand harsh temperatures and pressures. Precision-crafted screws improve material flow through reduced power consumption. This strategy ultimately boosts the efficiency of the extrusion process as a whole.
Innovations by CHUANGRI SCREW in Screw Barrel Technology
CHUANGRI SCREW is the first to pioneer screw barrel technology, strongly geared towards performance as well as quality, which is strongly reflected through their extremely sophisticated manufacturing practices. An excellent example of such a practice would be their Bimetallic Screw, where the screw undergoes an intricate special alloy coating process. Such a process has a vastly enhanced durability level on the screw barrel, even surpassing standard nitrided barrels by tens of times. This particular technique not only amazingly enhances the life span of the product, but also incredibly enhances the processing capability of challenging materials. Such complex materials include engineering plastics and mixtures containing a high proportion of calcium carbonate.
Addressing Common Challenges in Extrusion Processes
Overcoming Wear and Tear Issues
In the CHUANGRI SCREW extrusion operation, to control wear and tear is a challenge that can make a significant difference in equipment lifespan and efficiency. Using high-quality materials like 38CrMoAlA for their extruder screws and barrels helps to improve durability. With the addition of processes like nitriding or bimetallic processing, it has better wear resistance compared to standard nitrided barrels. BimetALLIC barrel used in a single screw extruder is coated with an alloy layer on the inner wall of the barrel to provide exceptional resistance to corrosion and wear, it also can operate at high temperatures effectively for a long period.
Troubleshooting Common Extrusion Problems
Extrusion processes may face a range of challenges such as product quality and equipment malfunctions which can be quite troublesome to handle at times for sure. Through inspections during each production phase and rigorous testing procedures backed by cutting-edge design tools, like AutoCAD and Solidworks. CHUANGRI SCREW ensure that every single component is finely tuned for optimal performance and rock-solid reliability. Taking steps helps reduce disruptions and ensures that the result remains reliable and consistent.
FAQs with CHUANGRI SCREW Experts
Q: What sets CHUANGRI SCREW extrusion screw barrels in terms of durability compared to others?
A: CHUANGRI SCREW utilizes high-quality materials like 38CrMoAlAm. Employs techniques such as nitriding and bimetallic processing to improve longevity and durability resulting in enhanced wear resistance when compared to regular nitrided barrels. For example, PVC with high calcium carbonate could reduce wear from abrasive additives. And the alloy coatings maintain structural integrity under extreme mechanical and thermal stress. Screws and barrels are tailored for materials such as high-filler polymers and recycled plastics.
Q: What choices for personalization are available for extrusion screws at CHUANGRI SCREW company?
A: CHUANGRI SCREW offers a variety of customization options to create extrusion screws that match the characteristics of different materials and production requirements effectively ensuring top-notch performance across various applications. Spanning from common plastics to advanced materials such as PPO and fluoroplastics. Custom packaging solutions based on client preferences is provided. They also offer a range of accessories. Integration of components like pins, vents or mixing zones to optimize processing efficiency.